Brief:
A simple and reliable screw switch that's easy to make.
Construction:
This is my design for a screw switch.
Materials:
- Scrap of double-sided PCB, about 1" by 1/4". I got mine from a Radioshack PCB Etching Kit (part# 276-1576), but you don't need the kit for this project. Part# 276-1499 is just the board. Digikey part# PC41-ND or similar will also work.
- 3 machine screws. Two long enough to mount the switch to the airframe, and one about 3/8" long (longer is OK).
- 3 nuts for above screws. The hardware can be either #4 or #6, it's up to you. I used zinc-plated, and it soldered just fine. Other metals might be harder to solder.
- Solder. You will be soldering one of the nuts to the PCB, so you don't want solder that's too thin. Also, you might need some flux if the solder won't flow onto the nut very well.
- Some wire for leads. Speaker wire or something similar will work.
Tools:
- Soldering iron. Anything should work for this application. A small one will take a while to get the nut up to temperature, but you don't have to worry about any heat-sensitive components here. I like my temperature-controlled Hakko soldering station, but it's not necessary for this project.
- X-Acto knife with a blade you don't mind ruining
- Drill with a drill bit big enough for a clearance hole (1/8" for #4, 5/32" for #6), and a small drill bit (maybe 1/16"). The PCB material will wear out bits quickly, so take it slow and use an older bit if you have one.
- A vise or something to hold the board while you are drilling/soldering.
- Tools to cut the PCB. Many things will work--a Dremel with a regular or diamond wheel, a hacksaw, or even an X-Acto knife to score the board them pliers to snap it (you might not get good results this way).
Procedure:
- Cut a piece of the PCB. It needs to be wide enough for the screw heads and the nut, and long enough for 3 screws to fit in a row with enough space in between to not get a short-circuit.
- Scrape off 1/3 of the copper on each side (see diagram), using the X-Acto knife (be careful!). The proper technique would be to etch it, but that is a more complicated and messy procedure.
- Drill 3 large holes, as shown in the picture.
- Drill the 2 smaller holes for wire leads.
- This step is slightly tricky. You need to solder the nut to the PCB on one side. To do so, thread the nut onto one of the screws so it holds the nut against the PCB. Now, heat up both the nut and the PCB with the soldering iron. Do not overheat the PCB or you could melt the glue layer and make the copper lift, which will make an unreliable joint. Once everything is hot enough, apply some solder all around the base of the nut where it touched the copper. If everything goes well, the nut should be attached to the board by a small fillet of solder. If solder is not sticking to the nut, you might need to clean it, use some flux, or get a nut made of a different metal. Don't use too much solder or you will solder the screw inside the nut, making it impossible to remove once cool. Once everything cools, remove the screw that was holding the nut in place. It should come out easily.
- Now, on the other side, add a ring of solder to give the screw head something to bite into when you tighten it down. Solder is somewhat soft, so it will keep the copper from being damaged.
- Next, solder a wire into each of the small holes from the bottom, making sure that the wire is actually soldered to the copper, not just stuck in the hole with solder.
- Test the switch (hooking it up in series with a light bulb and a battery should be sufficient).
- Attach the switch to the airframe using the remaining screws. You will need to drill a larger hole under the center hole (where you soldered the nut) so the switch sits flush. You can also pass the wires through the same hole.
- Add fillets to make it a little more aerodynamic. I used wood filler, but you can also use epoxy, Superfil, Bondo, etc.
The only thing left is to hook up the switch to the altimeter and ground-test everything. It's OK to tighten the screw fairly tight since with this design, pressure squeezes everything together rather than pushing everything apart. With enough force, you might strip out the nut, but it's not likely.
Pictures:
I made the renderings with Google Sketchup and the diagram with NeoOfficefor Mac. (Note: Windows and Linux users can use OpenOffice.org.)
Top view:
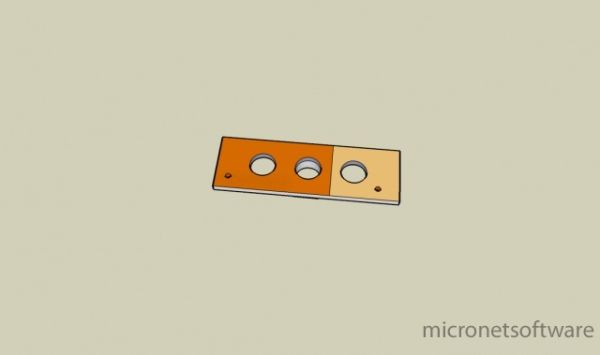
Bottom view (magic flying switch):
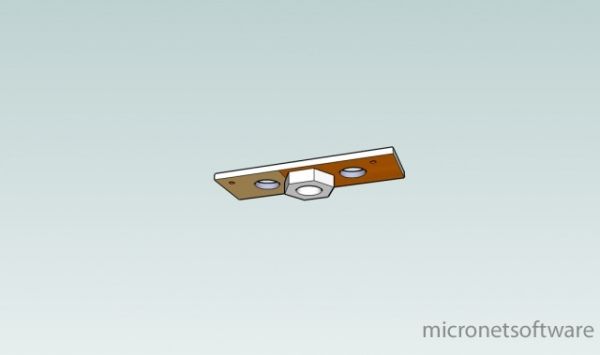
Side diagram: