(Contributed
- by Donald Qualls)
Luna 2-18 Express
Model designed and built by Donald Qualls
The Heinlein Fleet entered service in 1991 with the launch of the
Terra. The class eventually
consisted of eight ships, and served with distinction on suborbital, orbital,
and transLunar routes until being phased out of first line service in favor of
newer, more efficient designs beginning in 2019. The ships continue in second
line and feeder service to the present day. Powered by twin Dumbo 18 nuclear
engines, the 2-18 Expresses were capable of single stage operation round trip
from Earth to the Lunar surface with a full passenger complement, or heavy lift
operation to orbit or suborbitally. Equipped with belly jets as well as wings,
they could be flown off the ground horizontally (with 65% propellant load) from
simple concrete runways, short landed in less than two kilometers, boosted in
landing attitude under Lunar gravity, or hoisted and launched vertically from
towers like older transport designs for maximum delta-vee.
TheLuna, second in class, is
famous not for what she did in her original role, but for what she was called
on to accomplish after she was officially retired. Purchased as scrap after
being taken off the Lunar route by Pan Am Cunard in 2021, she was refitted for
long endurance, her engines modified to use any combination of water, methane,
or ammonia (or, in practice, nearly anything that would liquify at tank
pressure and temperature) instead of Single-H (stabilized monatomic hydrogen),
and catapulted from the then-new Farside Facility to carry the first manned
mission to the outer planets. After four years exploring the Jupiter system,
scooping reaction mass from the atmosphere of the giant planet at intervals of
a few months, she was lost with all hands, presumably to a meteoroid impact,
during transit of the main Belt en route back to Earth.
Despite her tragic end, the
Luna proved beyond any doubt that the 2-18 Express class was
capable of far more than their designers envisioned. The
Luna made the entire expedition
possible, since her combination of low cost, high capacity, and excellent
record meant money could be saved for other things; without the lucky find, the
mission would have had to be postponed, possibly for many years, while more
funds were raised and a ship built.
-- Jane's All the System's Spaceships, 2060 edition
Here we see a model of this most famous member of the Heinlein Fleet, the
Luna 2-18 Express. I have chosen to model the ship after she was
retrofitted with
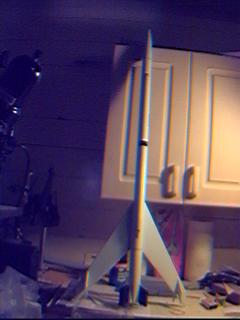
propellant scoops and her passenger
cabin converted to long term living quarters and hydroponics. During that
process, in order to save mass that would contribute nothing to the mission,
her belly jets and landing gear were removed and her main propellant tank
extended an additional 14 meters past the original nose (just below the
cockpit, the original nose faired into the passenger cabin's hump); this gave
enough propellant capacity, in conjunction with the Farside Facility catapult
launch, to transit directly to Jupiter the catapult could not be used
for a slingshot maneuver around Earth, and the propellant used to boost from
the Lunar surface or direct from Earth orbit would have been sorely missed
during Jovian insertion.
Clearly visible on the model are the distinctive twin nuclear-thermal Dumbo 18
engines, uprated and improved versions of the first nuclear engine to boost
from the Earth's surface. While less efficient in deep space than the older
Nerva design, the Dumbo engines were capable of far more thrust, and were more
tolerant of variations in propellant and the introduction of Single-H in
1986 brought the Dumbo engine's efficiency up enough to make single stage Lunar
round trips economically feasible.
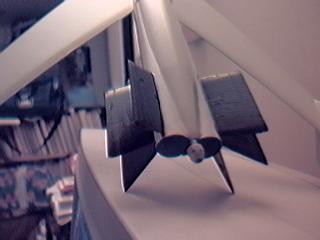
The distinctive aeroshell around the forward ends of
the engines houses the propellant pumps and the power reactor, a liquid sodium
power plant adapted to provide electricity for the 2-18 Express. This
all-nuclear system meant the 2-18 class didn't need to carry any oxidizer; the
Single-H could be catalyzed to recombine and provide very effective maneuvering
and landing jets, and of course was the best possible propellant for use in any
nuclear thermal engine. Simplified plumbing and a single tank meant still more
performance improvements over older designs and like everything else in
aerospace, once you start saving a little mass somewhere, the savings snowball.
In her heyday, the Luna carried 42 passengers and a crew of five (three
flight crew and two attendants) on the 60 hour run to the Moon, though
suborbital flights of less than an hour saw coach grade seating exceed 130
passengers after the ships were retired from first line service. The 2-18
Express class was also the first type to have extensive on board computing
capacity; the originally installed computers were upgraded several times
through the years, but even the first model had more computing power in the
cockpit than was used to calculate the Galileo's course on her historic
Lunar voyage. By the time of her Jovian mission, the Luna's main
computer was capable of speech synthesis and recognition and was more like one
of the crew than a tool or appliance.
The Model
This model was designed to be as accurate as possible and still be easy to
build. The main propellant tank is twenty-seven inches of BT-56, the passenger
cabin is
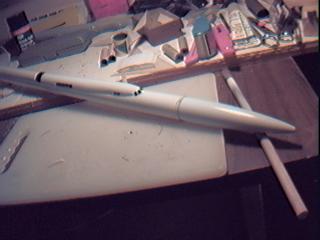
made from 18"
of BT-50 split lengthwise with a BNC-50A (Alpha nose cone) split and
carved/sanded to fit the contour of the BT-56. The nose cone and aeroshell are
from a Maniac and a Long Shot the aeroshell was split along the molding
seam and carved to fit the contours of the dual motor mount, then glued to the
airframe and motor mount tubes with medium CA. A small liberty was taken; I
installed a positive retention system to ensure that the motors stayed in place
and did their job at deployment time. Unfortunately, due to a camera problem
(the operator failed to secure the film to the take up spool when loading,
resulting in a blank roll), there are no construction or flight photos; only
these images, taken with a web camera, currently exist.
There's a simple baffle incorporated into the forward end of the motor mount.
It consists of a couple inches of BT-5 mounted into each BT-20 motor mount with
a 520 centering ring; by happy coincidence, this places the BT-5 at exactly the
spacing they'd have if they were part of the four-tube cluster that can be
mounted in a BT-56; that lucky spacing allowed me to overlap the forward ends
of these tubes with the aft ends of another pair occupying the other two
positions of the cluster tube, with the result that ejection gases have to
double back twice in order to reach the main airframe -- this does a very fine
job of trapping any hot particles; in three flights, it was difficult to see
from the parachute and shock cord that any ejections had occurred. If you
choose to incorporate the baffle, however, I'd recommend making the baffle
tubes longer than I did to improve the ease of aligning the motor mount with
the airframe.
The wings are mounted at 15 degrees anhedral that is, drooping slightly.
The wing planform is a 60 degree leading edge sweep, tapering from a 6 inch
root edge (this can be cut from 3 inch wide fin stock) to a two inch tip, in
1/8" balsa. The rudder fins are mounted far enough inboard that there's a
flat fin surface to glue to on the original ship, the ventral fins would
hinge outward, flat to the bottom of the wing tip, to provide ground clearance
for landing. I haven't modeled the belly jets or landing gear, of course,
because they were removed during the refit to this configuration, but you can
see the propellant scoops, in their retracted position, at the extreme forward
end of the engine nacelles.
Radially mounted on the aft ends of the nacelles are the radiators for the
electric power reactor; these dump waste heat overboard by radiating it away to
space or conducting it to the atmosphere. As you can see, they're mounted in
such a fashion as to minimize the amount of exposure to each other, in order to
get maximum efficiency with minimum mass; they're modeled in 1/16" balsa.
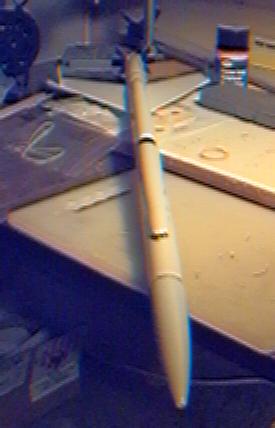
The issue of paint schemes is a sensitive one
the
Luna originally wore the Pan Am Cunard colors, but that paint scheme
wasn't preserved when she was taken out of service, and the extensive refit
prior to the Jupiter mission didn't originally include a repaint paint,
again, was excess mass. The actual color scheme, then, is a combination of
whatever was left of the original PAC and whatever natural finish was present
on new parts (such as the propellant tank extension and ram scoops) the
latter frequently bare metal, since the ship wasn't expected to need protection
from oxidation.
Just before launch, however, someone pointed out that publicity images would
show the ship in a bad light, looking like something jury rigged from a wreck
instead of a pioneer, so the expedition management had a fast coat of whatever
they could find applied to cover the refits, with no expectation of good
adhesion due to complete lack of surface preparation. Unfortunately, the only
images of the ship in this configuration are those publicity shots so
that's the color scheme I've modeled, a plain white hull and wings, flat black
radiator surfaces, and whatever windows were left after the refit. The dark
band just aft of the nose, unfortunately, isn't part of the modeled color
scheme -- it's the minor damage from a core sample on the first flight of the
model.
Flight Report
Recommended motors: 2x B4-4, 2x
B6-4, 2x C6-5
Building -- Parts and Plans
To built the
Luna 2-18 Express you'll need the following parts:
27" of BT-56
1 or 2x BT-56 couplers (mine came with an 18" section in the bag, so I
only needed one coupler, but the standard length seems to be 9" and will
need two)
2x PNC-56, same as those in the Maniac and Long Shot kits
18" of BT-50 (for passenger cabin)
1 BNC-50, balsa version of an Alpha nose cone (plastic will work also, but it's
a bit harder to split and sand to contour)
2x 6" sections of BT-20
4x 520 centering rings -- two for the baffle, two as thrust rings
4x 4" (or longer, as desired) sections of BT-5 -- or only two if you don't
build the baffle
Card stock for cutting the gas seals on the baffle
1 sheet 1/8" balsa, 3" wide, medium-hard
suitable scrap or sheet of 1/16" balsa at least 1.6" wide, medium
3/16" launch lug
Recovery system of your choice (I used a 14" Quest parachute left over
from my Big Betty's conversion to an egg lofter)
Optionally, some sort of motor retention system
Please see the following fin alignment diagram, including baffle layout, and
dimensioned fin pattern:
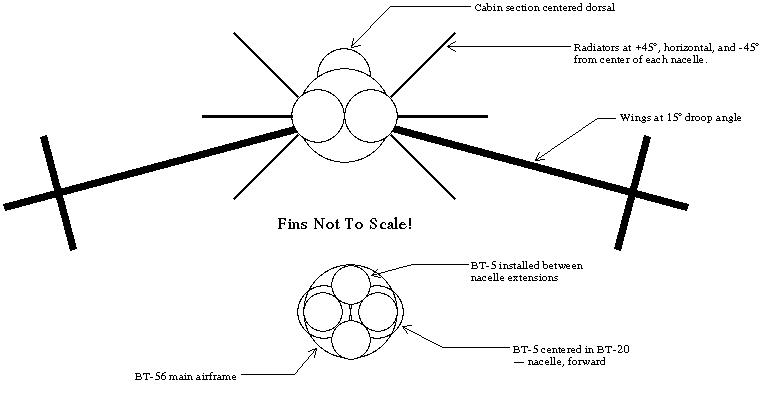
Click to Enlarge
To construct the Luna 2-18 Express model, first join the sections of
BT-56 airframe. Ensure that the sections are straight by rolling the tube on a
flat surface such as a table top before the glue sets. Set aside one nose cone,
it will be the actual nose cone. Split the other nose cone along the molding
seam, and remove the base of the "heel" section of the cone. Cut the
heel section to about 1/4" length -- this is not a critical dimension,
this cut just simplifies fitting the aeroshell later one.
Sand the glassine off all the tubes to facilitate glue adhesion -- doing
this now will avoid frustration later.
Mark the motor mount tubes for the locations of the radiator fins and for
their glue join line. Install the 520 centering rings, two as thrust bearings
about 2 1/2 inches from the rear of the tubes, the others exact at the forward
ends of the tubes. Glue one BT-5 section into each forward centering rings,
taking care to align the BT-5 parallel to the BT-20. Join the two BT-20 tubes
side by side, with both BT-5 at the same end. Placing the tubes on a flat
surface like a table top while gluing will help ensure the motor mounts are
parallel.
If you're making the baffle, cut the centering rings to fit the BT-56 and
the BT-5 baffle tubes, and assemble the baffle as shown in the diagram -- the
BT-5 for the forward half should overlap the BT-5 from the motor mounts by
about one inch, to allow for good gluing. Start by sliding one centering ring
onto the BT-5 in the motor mount, leaving about 1/2" clearance from the
motor mount to allow for attaching the aeroshell later; glue it in place. Slide
the other centering ring over the other pair of BT-5, apply glue, and then glue
those tubes to the tubes from the motor mount to for a cluster of tubes with
about an inch of overlap and a baffle chamber with adequate space to avoid
restriction of the ejection gas. Be very careful of alignment; roll the
assembly on a table with the motor mounts hanging off the side to ensure it's
all straight. Once the glue is dry, mount the assembly into the BT-56 airframe,
butting the forward end of the BT-20 against the aft end of the BT-56. If
you've built everything straight up to now, the motor mounts will align
parallel to the airframe; if not, you can flex the mount a bit at this stage,
and when the glue sets up where the BT-5 contacts the inside of the BT-56, it
will lock your adjustments in place.
Once the glue is dry, carefully carve each half of the split nose cone to
fit the contour of the motor mount tubes. The aeroshell halves must lie along
the motor mount tubes and the shoulder end must fit into the airframe. Once you
have a good fit, glue the aeroshell in place. If you'll be using a motor
retention device or system, be sure to install it before permanently mounting
the aeroshell, as you won't be able to afterward.
Cut all the fins. Plane and/or sand the main wings to a symmetrical airfoil,
then do the same for the rudder fins and radiators. Use your choice of methods
to fill the grain and tube spirals; I used Finishing Wood Filler before gluing
the parts together, but everyone has their own preference. Attach the wings
first, then put the rudders on the wings, and finally attach the radiators to
the motor mount tubes. If you use double glue technique, white glue is more
than adequate, though I recommend you use a sling type shock cord attachment to
lower the rocket horizontally or slightly nose down. Don't forget to fillet --
those are very, very large fins with a surface mount.
Once the fins are in place, mark the BT-50 full length on both sides, and
carefully split it along the mark. If you use a metal angle or channel as a
guide, beware of the tube closing up after the first side is split, and leaving
you with a helical second cut -- this is bad. Split the BNC-50 and glue the
halves into the ends of the split tube. Use the airframe to mark the arc on the
butt end of the nose cone halves, and then use a gouge or power sander to rough
cut before sanding to final fit. Glue the passenger cabin to the airframe,
ensuring the BT-50 is adhered all along both edges. Fillets here are cosmetic,
but they have a big effect on the appearance of the model.
Hang in there, you're almost done! All that's left is filling and sanding,
if you haven't, attaching the launch lugs, installing the recovery system, then
finishing by your choice of methods. Now go fly!